Compositeplatten in Wabentechnologie: leichte und stabile Bauteile von 3M
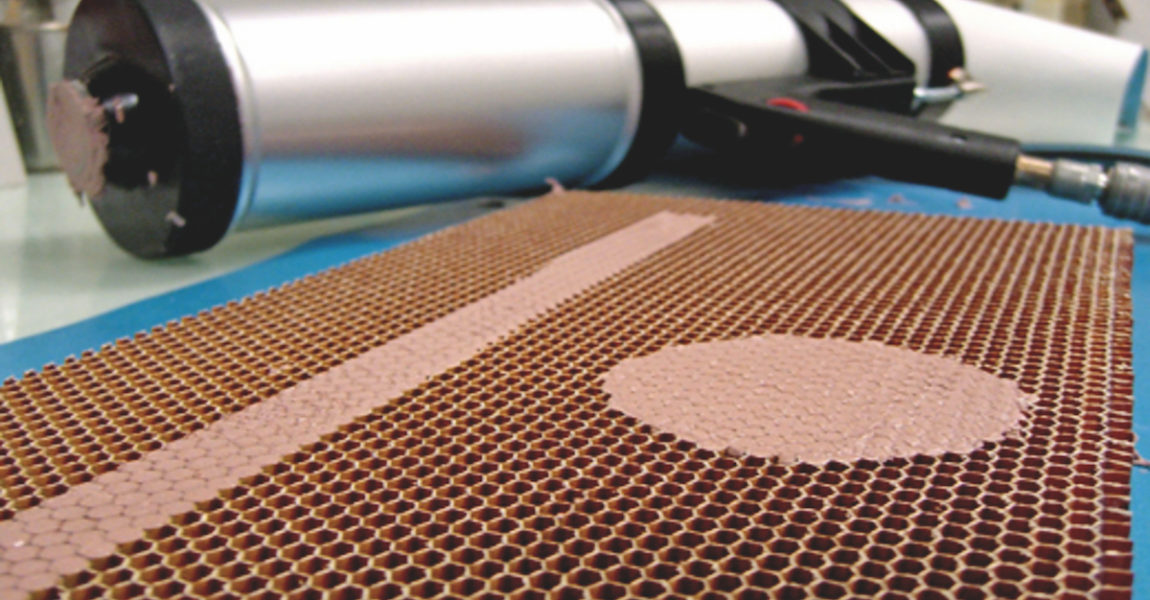
Beim Kabinenausbau sorgen Compositeplatten in Wabentechnologie für leichte und stabile Bauteile. Sie dauerhaft miteinander zu verbinden, erfordert exakt abgestimmte Klebe- und Füllstoffe – die Luftfahrtsparte des 3M-Konzerns hat sich darauf spezialisiert
Der Name ist an Sachlichkeit kaum zu überbieten: „Rand- und Kernfüllmasse EC-3505 B/A FR“. Sie haben keine Ahnung, worum es dabei geht? Und Sie wissen auch nicht, wer die Minnesota Mining & Manufacturing Company ist? Das ist Ihnen nicht zu verdenken. Und doch geht es um ein Riesenunternehmen, das im Alltag der meisten Menschen eine Rolle spielt – und um eines der Produkte der Firma, die in der Luftfahrt immer wichtiger werden. Also zählen wir Anfangsbuchstaben: 3M!
Genau so heißt die 1902 als Bergbauunternehmen gegründete Firma heute. Deren nicht richtig klebende und genau deshalb so praktische Notizzettel namens „Post-it“ haben Sie garantiert schon mal benutzt, damit etwas nicht in Vergessenheit gerät. Da ist die anfangs erwähnte Kernfüllmasse schon deutlich unauffälliger. Doch dazu später mehr. In der Luftfahrt ist 3M schon seit langem ebensowenig wegzudenken wie die gelben Klebezettel im Büro. Denn seit über 50 Jahren wird im Flugzeugbau nicht nur genietet und geschraubt, sondern an vielen Stellen auch geklebt – und das ist ein Spezialgebiet des US-amerikanischen Multitechnologiekonzerns.
Eineinhalb Jahre Entwicklung
Vor allem beim Innenausbau ist dabei die Tendenz steigend – und das nicht nur, weil Klebstoff potenziell leichter ist als Schrauben und Niete. Der Grund ist unter der Oberfläche zahlreicher Kabinenelemente versteckt: Das Innere von Wandverkleidungen oder Schrankwänden besteht aus einem Kern, der im Englischen treffend „Honeycomb“ heißt: Honigwabe. Die Wabenstruktur wird auf Ober- und Unterseite mit einer Deckschicht versehen, sodass eine Sandwichstruktur entsteht. Sie ist stabil und gleichzeitig leicht – was die Bauweise gerade für die Luftfahrt so interessant macht. Mit wenig Materialeinsatz lassen sich so Platten für Kabinenwandverkleidungen, Fußbodenpaneele oder Gepäckfächer herstellen – kaum ein Passagier weiß, dass die Technologie in so gut wie jeder Kabine versteckt ist.
Bei der Verarbeitung müssen die Flugzeugbauer jedoch andere Wege gehen als traditionelles Nieten und Schrauben: Die halten nämlich in der Wabenstruktur nicht. Also werden die Verbundplatten verklebt. Für nahezu jeden Anwendungsfall ist dabei ein anderes Klebemittel erforderlich – je nachdem, ob Platten verbunden, Befestigungsklammern montiert oder Oberflächen aufgebracht werden sollen. So findet auch die anfangs erwähnte „Rand- und Kernfüllmasse“ ihre Anwendung: Sie basiert auf Epoxidharzen und wird eingesetzt, wenn Bereiche eines Sandwichelements zusätzlich verstärkt werden müssen – indem die Waben im Kern der Struktur aufgefüllt werden.
Ebenso lassen sich damit die Kanten einer Platte versiegeln und damit vor dem Eindringen von Feuchte schützen. Damit der Gewichtsvorteil dabei nicht zunichte gemacht wird, muss die Füllmasse möglichst leicht sein. EC-305 B/A FR wiegt gerade einmal 440 Gramm pro Kubikmeter. Das gleiche Volumen Wasser bringt es auf eine Tonne. Mit diesem Wert ist der Füllstoff nochmals zwanzig Prozent leichter als Produkte, die zuvor verwendet wurden. Eineinhalb Jahre hat der 3M-Entwickler Sohaib Elgimiabi an dem neuen Produkt gearbeitet, bis es praxistauglich war. Beteiligt waren unter anderem Techniker und Maschinenbauer aus Deutschland und Kanada.
„Nach der Verarbeitung war das Produkt wieder sehr viel schwerer als bei der Lieferung. An dieser Schraube mussten wir lange drehen“, sagt Elgimiabi. Einer der ersten Kunden des Produkts ist der kanadische Flugzeughersteller Bombardier. Dessen Geschäftsfliegersparte setzt es beim Innenausbau seines Flaggschiffs ein, dem kürzlich zugelassenen Businessjet Global 7500. Weil sich die Füllmasse auch noch besonders schnell aus Kartuschen verarbeiten lässt, hilft sie dem Hersteller nicht nur Gewicht zu sparen, sondern auch die Produktivität zu steigern. Brancheninsider, die es noch genauer wissen wollen, haben auf der Fachmesse für Flugzeuginnenausstattung AIX Gelegenheit dazu: Vom 2. bis 4. April ist auch 3M dort vertreten.
Text: Christof Brenner, AERO INTERNATIONAL 4/2019