Flugzeugteiletransport per Beluga und Dreamlifter: Werkverkehr bei Airbus und Boeing
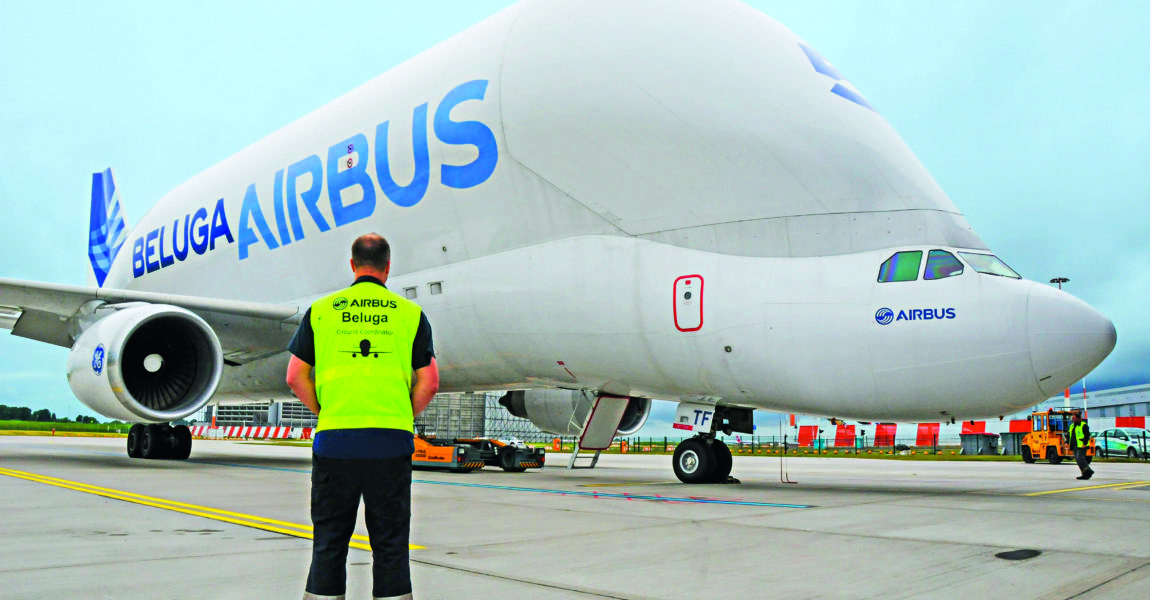
Wenn heute bei Airbus oder Boeing ein Flugzeug die Werkhalle verlässt, ist das nur durch ein komplexes Räderwerk von Transporten möglich, die exakt ineinandergreifen
Eine nicht ganz ernstgemeinte Definition des Begriffs „Flugzeug“ lautet: fünf Millionen Teile im engen Formationsflug. Das große Kunststück ist, diese Teile so rechtzeitig zusammenzubringen, dass am Ende ein Flugzeug aus der Halle rollt, und zwar zu dem mit dem Kunden geplanten Termin. Rund 800-mal pro Jahr passiert das bei Airbus, dreimal an jedem Arbeitstag. Und jedes dieser Flugzeuge ist das Ergebnis einer logistischen Meisterleistung. Längst gibt es erste Überlegungen, wie Airbus über 1000 Flugzeuge pro Monat schaffen könnte. Schließlich kommen seit Jahren mehr Bestellungen rein, als Flugzeuge ausgeliefert werden. Inzwischen stehen über 7000 Aufträge in den Büchern, die Produktion von neun Jahren bei heutiger Geschwindigkeit.
Die komplexe Logistik der Flugzeugteile
So lange wollen die Airlines nicht warten. Auch die Aktionäre freuen die vielen hundert Milliarden Euro, die all diese Verträge wert sind. Sie aber möchten sie lieber heute als morgen in echten Umsatz und in Rendite umwandeln. Aber je höher die Taktrate, desto höher die Latte für die Logistiker, desto mehr kommt es darauf an, dass wirklich jedes Rädchen im Getriebe des hochkomplexen Produktionssystems mit seinen zahllosen Beteiligten reibungslos funktioniert. Denn das Ganze soll natürlich möglichst ohne teure Erweiterungen der Produktionsanlagen passieren. Mit jedem Flugzeug mehr, dass durch das System gepresst wird, sinkt der Spielraum für Fehler. Ein Verkehrsflugzeug zu bauen, ist ohnehin kompliziert.
Einen Airbus herzustellen, war aber schon immer etwas komplizierter. Die heutige Unternehmensstruktur mit ihren Hauptstandorten in Deutschland, Frankreich, Großbritannien und Spanien geht auf die Zeit zurück, in der die beteiligten Staaten für jeden neuen Flugzeugtyp einen genau bemessenen Arbeitsanteil für ihre eigene Industrie aushandelten. Das führte natürlich zu einem über ganz Europa verzweigten Netz von Produktionsstandorten, zumal in jedem Land ebenfalls eine Vielzahl von Unternehmen zu beteiligen war, von denen die weitaus meisten heute in dem großen europäischen Ganzen namens Airbus aufgegangen sind.
Wenn in Hamburg-Finkenwerder oder Toulouse eine A320 aus der Endmontage rollt, dann haben ihre wichtigsten Komponenten bereits ein paar Flugstunden auf dem Buckel. Unermüdlich sind die fünf Airbus A300-600ST, besser bekannt als Beluga, unterwegs, um zwischen den verschiedenen Airbus Standorten Flügel, Rumpfsektionen und andere Großbauteile der verschiedenen Airbus-Typen zu transportieren: Flügelrohlinge aus Broughton in Wales, fertig ausgerüstete Flügel aus Bremen, Rumpfsektionen aus St. Nazaire, Flügelmittelkästen aus Nantes, Höhenleitwerke aus Getafe.
Werktransport – Per Luft, See oder Schiene
Ab 2019 erhalten sie Unterstützung von der neuen und größeren BelugaXL. Betrieben werden die Flugzeuge von der eigens für diesen Zweck gegründeten Frachtfluggesellschaft Airbus Transport International. Rund 2000 Stunden ist jeder Beluga pro Jahr in der Luft. Fünf Flüge pro Tag an sechs Tagen in der Woche sind als Pensum für jeden der Transporter eingeplant. Das ist ein strammes Programm. Da muss es am Boden ruckzuck gehen mit dem Ein- und Ausladen. Damit das schneller als früher klappt und so die Zahl der Flugstunden pro Jahr verdoppelt werden kann, hat Airbus überall, wo die Beluga Großbauteile anliefert, neue Beladestationen gebaut.
Diese sind im Konzept einheitlich, aber natürlich auf die Besonderheiten des jeweiligen Standorts angepasst. Sobald eine Beluga in Hamburg gelandet und vor das Gebäude mit der Ladestation gerollt ist, wird sie von einem Spezialschlepper mit der Nase voraus in die Beladestation gezogen. Dann schließen sich die rund 20 Meter hohen Tore passgenau um den vorderen Teil des Rumpfs. Flügel und Heck bleiben draußen und mit ihnen Wind und Wetter. Früher hieß es bei 30 Knoten Windgeschwindigkeit abwarten. Grade im Winterhalbjahr ist so eine steife Brise in Hamburg, Bremen und Broughton durchaus keine Seltenheit. Jetzt aber gilt: Wenn der weiße Wal landen kann, dann kann er auch entladen werden.
Das schützt die Produktionsplaner vor unangenehmen Überraschungen, auch wenn die Natur mit ihren Unwägbarkeiten wie Nebel oder starkem Seitenwind bleibt. Sobald das Tor geschlossen und die Bremsklötze vor die Räder gezogen sind, wird das Nivellierungssystem am Bug installiert. Es sorgt dafür, dass der Laderaum des Flugzeugs und die Verladeeinrichtung der Halle millimetergenau auf einer Höhe sind und es auch bleiben, wenn die 17 Tonnen schwere Fracht von Bord ist. Gleichzeitig fährt das horizontale Interface Rack an den Rumpf und umschließt ihn konturgenau. Es ist die Schnittstelle zwischen dem Flugzeug und der Verladerampe. Dann öffnet sich das rund zwei Tonnen schwere Frachttor der Beluga und gibt den Blick frei in den riesigen sieben Meter hohen Innenraum. Bei über 1000 Beluga-Flügen im Jahr ist das alles perfekt eingespielte Routine.
Transporte per Zug
Diesmal kommt die Ladung aus Nantes, zwei A320 Rumpfsektionen hintereinander auf einem 35 Meter langen massiven Transportgestell. Nachdem sie entladen sind, rollt ein Satz A350-Flügelschalen aus Kohlefaser aus Stade, der schon bereitsteht, in den Bauch der Beluga. Er ist für das Werk in Broughton bestimmt, wo die Flügelrohlinge aller Airbus-Typen gefertigt werden. Im Zeitlupentempo kriecht der Transportwagen ferngesteuert unter den wachsamen Augen der Mitarbeiter in den Frachtraum und wird dort sorgfältig befestigt. Unterdessen bereiten die Piloten schon den Flug vor. Es gibt keine Minute zu verlieren. Nach nicht einmal zwei Stunden gibt das Hallentor den Flieger wieder frei.
Lange hat man beim großen Konkurrenten darüber gelächelt, dass Airbus halbe Flugzeuge kreuz und quer durch Europa fliegt. Ein typisches Beispiel für europäische Ineffizienz. Doch inzwischen setzt auch Boeing in der Produktion der 787 auf Lufttransport. Zu Dreamliftern umgebaute Boeing 747-400 versorgen die Werke in Seattle und Charleston nicht nur mit vormontierten Baugruppen aus Japan und Italien, auch innerhalb der USA zwischen Seattle, Wichita und Charleston fliegt das US-Pendant der Beluga. Aber dabei bleibt es dann auch. Die Rümpfe der 737 und Strukturbauteile für andere Flugzeugtypen, die von Spirit Aerosystems in Wichita produziert werden, treten die Reise ins 2300 Kilometer entfernte Seattle wie eh und je noch mit der Eisenbahn an. 2014 verunglückte so ein Zug in Montana auf dem Weg durch die Rocky Mountains. 18 Waggons entgleisten, drei der sechs 737-Rümpfe, die der Zug geladen hatte, stürzen einen Abhang hinunter in einen Fluss.
Per Schiff nach China
Nicht alles, was die Belugas in Hamburg für die A320-Familie anliefern, verlässt das Werk als fertiges Flugzeug auf dem Luftweg. Denn von Hamburg aus wird auch die Endmontage in Tiajin beliefert. Vom werkseigenen Anleger aus treten komplette Bausätze die einmonatige Reise in die chinesische Hafenstadt an: komplett ausgerüstete Rümpfe. In diesen fehlen nur noch Innenverkleidung, Sitze, Toiletten und Bordküchen. Dazu Fahrwerk, Höhenflossen und Seitenleitwerk. Während Rumpf und Höhenflosse nur einen grüngelben Korrosionsschutz tragen, ist das Seitenleitwerk bereits in den Farben des Kunden lackiert. Gehörten in den ersten Jahren auch die Tragflächen zu einem solchen Bausatz, so werden diese seit 2014 von XAIC vor Ort gebaut.
In Finkenwerder werden die auf speziellen Transportgestellen seefest verpackten Bausätze zunächst auf das 80 Meter lange Roll on-Roll-off-Schiff „Kugelbake“ gefahren, das sie im Hamburger Hafen abliefert, wo sie im Bauch eines Frachters der chinesischen Reederei COSCO verschwinden. Die Bausätze für das Werk in Mobile, die ihre Reise bis Mai ebenfalls ab Hamburg antraten, werden inzwischen von St. Nazaire aus verschifft. Das verkürzt die Seereise und damit die Lieferzeit um gut drei Tage. Mit etwas mehr als zwei Schiffsladungen pro Tag im Durchschnitt ist der Schiffanleger an der Elbe auch so gut ausgelastet. Zusätzlich zu den Seetransporten nach Übersee, die von Hamburg aus gesteuert werden, gibt es für die Schiffe immer mehr Arbeit innerhalb Europas.
Freie Kapazitäten an Bord
Seit Airbus sich bei der A380 angesichts der Größe der Baugruppen für den Transport per Schiff entschieden hat, ist dieses Element der Logistikkette immer wichtiger geworden. So sieht man die eigens für die Fahrt in Küstengewässern ausgelegte „Kugelbake“ regelmäßig in Nordenham an der Unterweser anlegen, wo sie aus dem dortigen Werk von Premium Aerotec Rumpfschalen für die verschiedensten Airbus-Typen lädt, die in Hamburg für den Bau von Rumpfsektionen benötigt werden. Und selbst die Zulieferung aus dem 25 Straßenkilometer entfernten Stade kommt zwischendurch per Flussfähre an.
Neben der „Kugelbake“ sind drei speziell für die A380-Produktion gebaute hochseegängige Schiffe mit dem Schriftzug „Airbus on board“ auf ihrem blauweißen Rumpf im Einsatz: die 127 Meter lange „City of Hamburg“, ihr Schwesterschiff „Ciudad de Cadiz“ sowie die mit 154 Metern etwas größere „Ville de Bordeaux“. Airbus will ihre Motoren in Zukunft mit Hilfe 1000 Quadratmeter großer Lenkdrachen unterstützen und so rund 20 Prozent Treibstoff sparen. Weil weit weniger A380 gebaut werden als einst geplant, haben diese Schiffe Kapazitäten frei, auf die die Logistiker in Hamburg gerne zugreifen. So wird die „City of Hamburg“ inzwischen regelmäßig eingesetzt, um Teile für die A330 und A350 aus St. Nazaire nach Hamburg zu schaffen.
Text: Heinrich Großbongardt, AERO INTERNATIONAL 1/2019